放電加工の歴史
放電加工は、1946年に旧ソ連のラザレンコ夫妻による研究が注目されてから一般に知られるようになりました。なんでも夫妻は、スイッチにおいて火花が発生し、接点が磨耗する現象を研究しているうちに新たな加工方法を思いついたということです。
日本における放電加工機の製品化は、1953年池貝鉄工所と日本放電加工研究所(JAPAX)により実現されました。ただし、当時の放電加工機は電極消耗が激しく、”抜き加工”にしか利用できませんでした。
現在の放電加工機のように、”底付き加工ができるようになったのは、1968年ごろトランジスタを利用した電源回路が実用化されてからのことです。その後、放電加工機は形状電極を使用して”底付き加工”ができる「形彫り放電加工機」とワイヤー電極を使用して”輪郭加工”を行う「ワイヤーカット放電加工機」の2タイプが主に使われるようになりました。
当社は、1987年に初めて放電加工機を導入しました。そして、2002年に、より高精度、高品質の加工ができるリニアモータ駆動放電加工機を導入しました。直彫り加工を広く行うようになった今も放電加工技術を研究しています。
超硬合金の加工に放電加工技術を用いる理由
【放電加工のメリット】
- 非接触の状態で加工し、高精度に仕上げることができる。
- 加工時にバリが発生しない。
- 被加工物が導体であれば、硬度、強度に関係なく加工できる。
近年、非導電性であるセラミックにも放電加工できるよう研究がなされている。
超硬合金は、非常に硬く、耐摩耗性・耐衝撃性に優れているため、金型や切削工具に広く用いられています。その非常に硬い超硬合金を加工するにはどうすればいいのでしょうか。導電性のあるものであれば硬さに関係なく高精度の加工ができる放電加工の出番となります。
超硬合金への形彫放電加工の難しいところ
超硬合金はその主成分であるタングステンカーバイド(WC)の融点が2900℃と高温であることから、加工に必要なエネルギーが大きいため、高いエネルギー密度の加工条件、言い換えるとピーク電流が高くパルス幅の短い条件が必要になります。
電極をほぼ無消耗で加工できる鉄鋼材料などへの形彫り放電加工とは違い、超硬合金の加工に用いられる加工条件下では、電極消耗が大きく加工精度の低下を招きます。そのため、銅タングステンや銀タングステン等の融点・熱伝導率が高い電極を用い電極消耗を少なくするとともに、消耗する量を加味して電極の設計や加工用のNCプログラムを製作します。
超硬合金への深穴加工
形彫り放電加工は、火花を断続的に飛ばし、金属の溶解・冷却・飛散を繰り返すことにより加工を進める非接触加工の一つです。そのためドリルやエンドミルを用いた切削加工などの接触加工とは違い電極自体には、それほど強度が必要ありません。
超硬合金などの硬い材質に大きな突き出し量が必要となってくる深穴加工を行うためには、硬さに関係なく加工でき、電極自体の強度もそれほど必要のない形彫り放電加工やパイプ状の電極を用い電極先端から加工液を出し加工屑の排出をしやすくした細穴放電加工が用いられます。
穴径の小さい深穴加工を評価する指標として、加工深さを穴の直径で割ったアスペクト比と呼ばれるものがありますが、直径0.1mm程度の場合はアスペクト比は10倍(深さ1.0mm)、直径0.2mm以上の場合は50倍(深さ10mm)のアスペクト比の加工が実現しています。
余談になりますが、上記のような高アスペクト比の加工するための電極製作にも、工作物に負荷があまりかからないという利点を活かし、ワイヤーカットや形彫り放電等の放電加工が用いられています。
超硬合金への異形穴加工
形彫り放電加工の特性として放電現象は角やエッジでより多く起こり、それらを持つ異形穴加工では、電極の消耗による加工精度の低下がより顕著に表れ、電極の設計・製作や加工そのものもよりシビアになります。
当社では、長年培われたノウハウやマシニングセンターなどの設備を用いた電極製作、熟練した職人の技により複雑な形状の加工を得意としています。
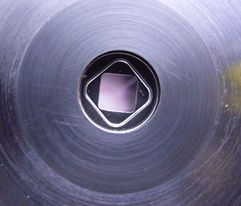