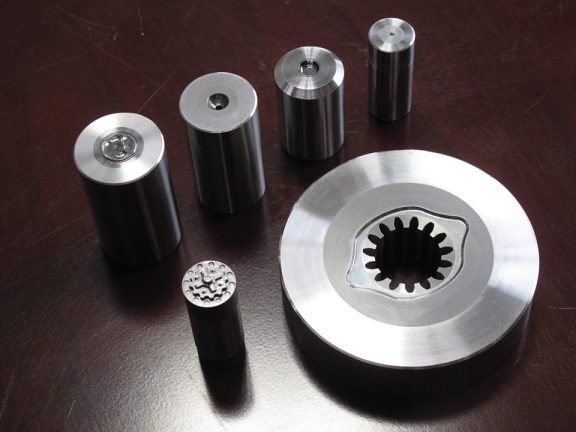
Tungsten Carbide, Tokyo Byora Koki Co., Ltd.
Dies lifespan extended 1.5 times
Applied “ Compressive residual stress” by direct carving
『Among high added valuing of manufacturing tendency, the cases which use a higher strength and higher heat resistant material are increasing.
Proportionally, a load to Dies is increased and the demand of Tungsten Carbide Dies which is superior to impact and wear resistance, is increasing.』said Mr. Hisamitsu Komi, president of Tokyo Byora Koki Co., Ltd.
The company is manufacturing cold heading dies to produce screw, rivet and electric contact.
Also precision press mold and extended wire dies are manufactured.
Among them, key product is a header dies.
Cold heading process which use those dies is a molding method to perform press drawing , upsetting process, and hollow process, and big merit is a speedy process.
Because of tough process condition, header dies are requested high level of impact and wear resistance and Tungsten Carbide,
WC-Co has been used widely.
Tungsten carbide which is called as super hard alloy in Japanese is extremely hard, rockwell hardness HRA 80-94.
Process method is mainly by EDM(Electric discharge machining).
Tokyo Byora Koki has purchased 8 sets of EDM and processing micro holes, variant holes and deep holes process and lapping process(mirror surface) by operator’s manual work.
However EDM has weak points of long process time, electrode is necessary, and micro crack which can be starting point of dies crack is easy to happen.
To overcome those weak points, Tokyo Byora Koki has challenged to direct carving process.
This is a decision to secure their survival.